- Name:
- Miho Iwata
- Profession:
- Wasaishi (Kimono Maker)
- Birthplace:
- Tochigi, Japan
- Current Residence:
- Asagaya, Suginami, Tokyo
- Web Site:
- http://harapecosmicooze.wixsite.com/iwatamiho (external link)
INTERVIEW WITH MIHO IWATA (KIMONO MAKER)
Miho Iwata, born in 1985, is a kimono maker. These days it is a rare job, especially among people of her generation. After an intensive five-year study, she established her own workshop at her residence at the age of 26. She implements “otoko-nui”, the traditional men’s style of sewing which uses not only hands but also feet as the third hand in sewing.
Experience Suginami Tokyo staff wanted to find out more about what drives a young woman to use such an old method in today’s modern technological age.
Experience Suginami Tokyo: There are not so many young people who choose to become a kimono maker. What made you decide to become one? Or what inspired you to become a kimono maker?
Miho Iwata: Actually, at first I wanted to become a Western style designer, but after my best friend chose to learn Western clothes design, I decided to learn something different, and that led me to continue on to Japanese fashion school. For most Japanese people, kimono is just clothing that we would wear during traditional ceremonies. But while studying kimono, I can see the charm of kimono. In Japanese society kimono are usually passed down from mother to daughter and so on, being taken care of through many generations. So, there is a historical and nostalgic element in kimono that I like.
EST: What are the hardships of being a kimono maker?
MI: I believe every job has its own hardships. For me, the hardest thing is when I am not satisfied with my sewing result. I feel disappointed when the result does not meet my expectations. But at the same time that also becomes a challenge that motivates me to keep going.
EST: I see that you use many traditional tools and a very unique technique, please tell us more about it and why you have chosen this method.
MI: As you can see, I work by myself, so I tried to keep everything simple and minimalist while using these tools efficiently. However, the tool I use the most is my own foot. It may sound strange but actually this technique has been practiced since long ago, and it has come to be called "otoko-nui" (which can be translated as "man`s sewing"). As the name hints, this technique was used by mostly men in the Edo period, particularly in Tokyo, as Kyoto (the place most famous for traditional kimono production) and Tokyo had different ways to produce Kimono. In the past, surprisingly many of the Kimono makers were men, because it requires some strength to hold the cloth and such. In order to save time they used their feet to hold and stretch the cloth. This technique allowed them to sew dynamically and faster. Despite some female kimono makers applying this technique nowadays, it is still referred to as “otoko-nui”. At first I was having a hard time mastering this technique, but after much practice, my leg can now work as my third hand. It`s very effective and time-saving, just as the kimono-making men in the Edo period realized.
EST: That’s very interesting, but why do use this old technique still today? With modern technology, why apply hand sewing instead of using a sewing machine?
MI: Recently, there are many kimono makers that turn to machinery for its efficiency and speed. But, I believe that using a sewing machine would harm the material as the needle pierces the cloth vertically. Moreover, because it uses two strings of thread to sew, it makes the cloth stiffer and harder to stretch. On the other hand, the hand-sewing technique uses only one string of thread and pierces through the cloth diagonally, which results in more stretchable kimono and will also be easier to modify in the future. These advantages are, of course, all in addition to keeping to the traditional aspects and charm of hand-sewn kimono.
EST: Do many Japanese people order custom-made kimono? Do you get many reservations monthly?
MI: I think that not so many Japanese people bother to have their own kimono specially made. However, there are some people who still appreciate the beauty and charm of traditional style hand-made kimono. I would say that I do not have a fixed amount of monthly reservations, as it fluctuates due to the season since most of my customers will order kimono for just special occasions.
EST: As an artisan who deals with kimono for your job, do take a special interest in kimono? How many kimono do you own?
MI: Good question. Unexpectedly, I own quite a lot of kimono. They are mostly old kimono that were passed down by my grandmother which I would modify. Sometimes I also buy old vintage cloth to make my own kimono. There are many modern style patterns nowadays, but I prefer the vintage patterns which I can get easily around Asagaya kimono shops.
EST: How long does it take to make one kimono?
MI: To make a kimono, there are some simple steps you have to go through first. For example, first and foremost we must choose the cloth. Some people submit their own cloth that they want to use and in some cases I assist in choosing the material and color that suits them best. Next, we take body measurements, then fix any strain of the cloth necessary and cut them before entering the sewing process. The sewing usually takes only 2 days. However, since there are so many other procedures before the final fitting, it takes roughly one week to finish. Also, since I work independently, when there are a lot of orders sometimes it may take up to two weeks.
EST: What are your plans for the future regarding your kimono-making business?
MI: I would like more people to know about traditional Japanese clothing. For the amount of work involved, kimono makers don’t exactly have a great financial situation. Due to that along with loss of interest among young people, it is said that the number of kimono makers is decreasing, and that this traditional craft may be lost. Therefore, I wish to spread the importance and appreciation of handmade traditional Japanese clothing so that the number of the kimono makers can increase in the future.
EST: Yes, it is often said that about kimono makers. That is why we wanted to interview you about it! We hope more young people will aspire to be kimono makers. Thank you for your time. Do you have any messages to our readers?
MI: Nowadays, there are many varieties of kimono materials and designs that foreign people can choose from. Yet, there are still few people who can have the chance to have their own kimono custom-made, which I think is more delicate and an amazing experience that people should try, especially if they are interested in Japanese kimono. So, if you are interested, please try to get one custom-made kimono. With great care, you can pass it to your child and grandchild and I believe it would become a very special treasure in your family.
[updated November 2018]
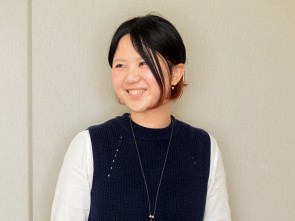
Miho Iwata-san
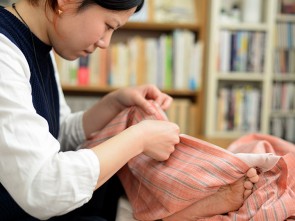
Iwata-san at work on kimono fabric
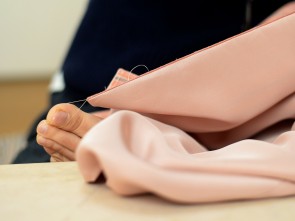
Using her toe to hold the fabric ("otoko-nui" method)
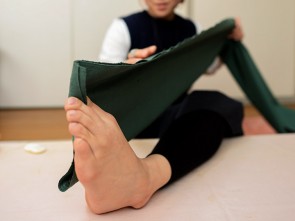
Her foot acts as a "third hand" to complete the work accurately and quickly
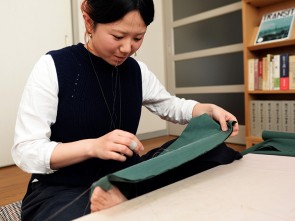
Thank you for demonstrating your technique, Iwata-san!